Our Projects
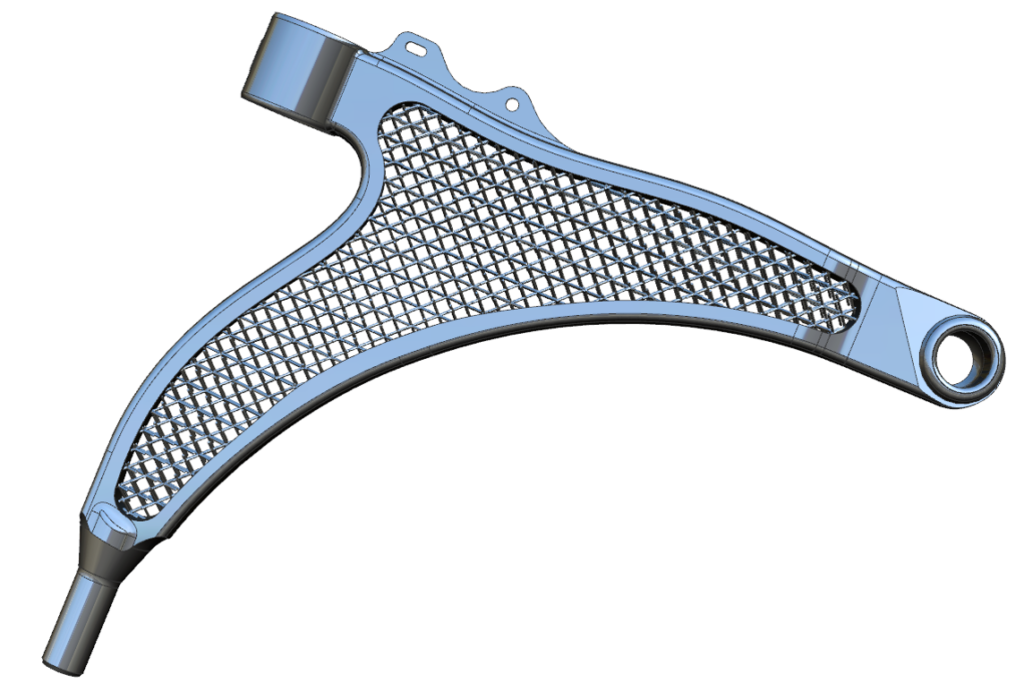
Support of DMLS 3D printing under multi-axis fatigue loading
Project co-financed by the Czech Technology Agency (TREND Program).
Focus: Support for DMLS 3D printing of metal parts under multi-axis fatigue – design, analysis, testing, and software development.
Partners: University of West Bohemia (Pilsen) & Slovak Technical University (Bratislava).
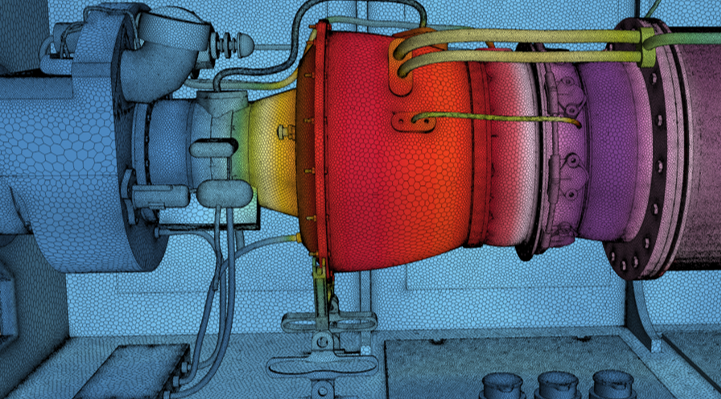
Turbine tightness analysis for hot state of turbine
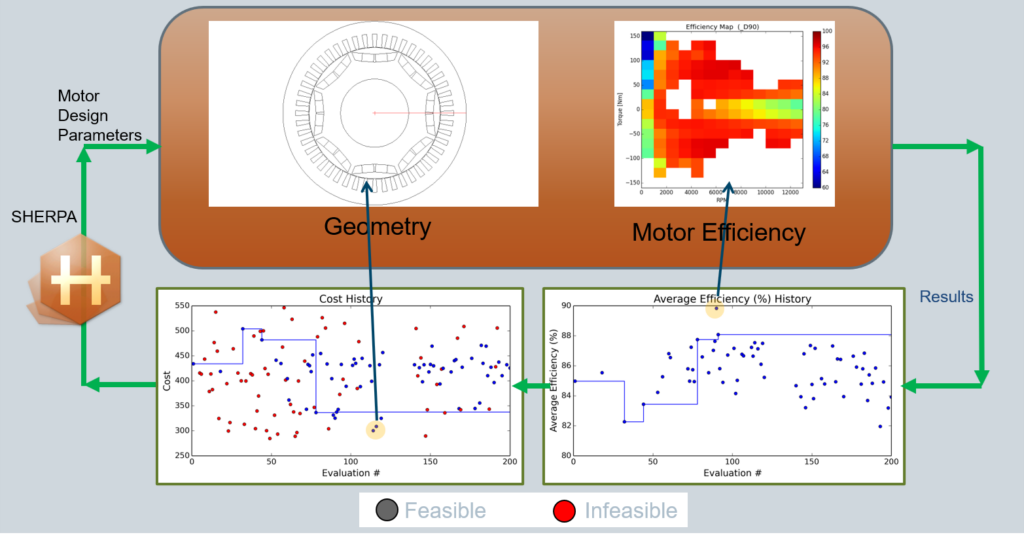
Optimization of electric motor for electric motor drive
Within the project, the synchronous motor with permanent magnets was optimized and the external rotor was designed for a racing electric motorcycle.
Simcenter MotorSolve software and HEEDS were used for the project.
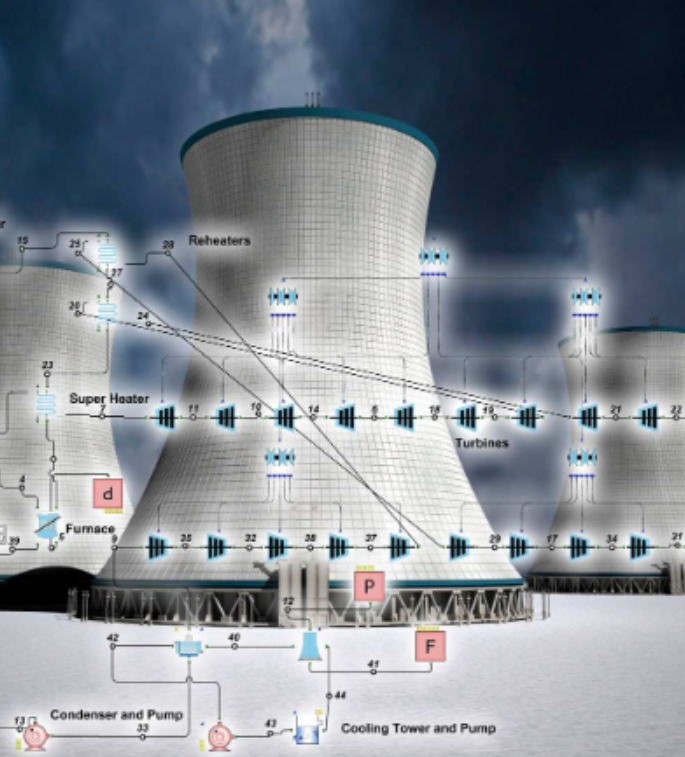
Hydraulic calculation of power plant cooling circuit
Within the project, a 1D system simulation of the cooling channel of the power plant was performed with the aim of calculating the pressure losses and flow rates throughout the system. All important elements such as pumps, fittings, elbows, etc. were included. An analysis of the level variation in the suction well during system start-up was performed.
Simcenter Amesim software was used for the project.
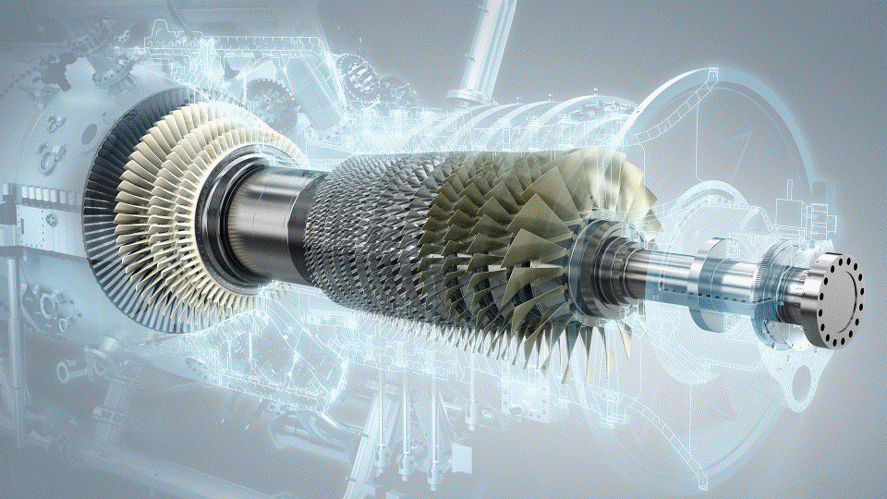
Stress analysis of generator exciter shaft
For the generator exciter shaft a stress analysis was performed for different sizes of shaft diameters at the points below the bearings. The aim of the project was to distribute shaft stresses and shifts for different shaft diameters and bearings with different stiffnesses. The project also included inspection of balancing pins.
Sicmenter 3D software was used for the project.
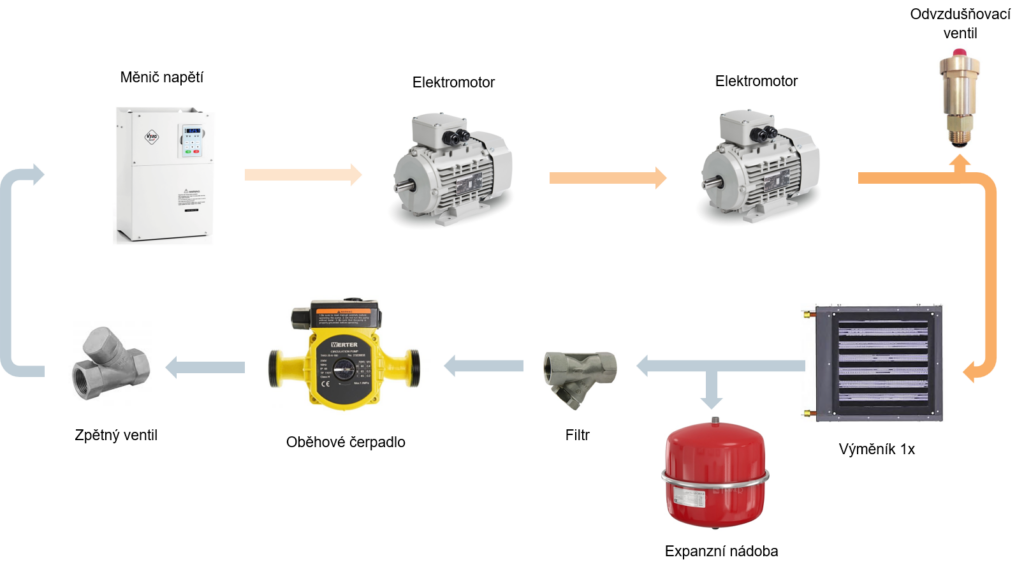
Design of cooling circuit 2 of series connected motors and inverter
The whole cooling system was created in the project based on system simulation. Based on the 1D calculation, suitable cooler / pump combinations for the cooling circuit were designed.
Simcenter Amesim software was used for the project.
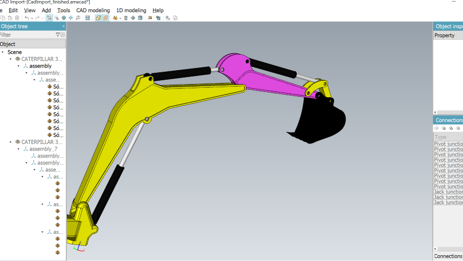
Prediction of service life of construction machine node
In the first phase of the project, a kinematic model of the construction machine node was created, which resulted in the calculation of the loading force arising from the impact. This was followed by a transient load analysis, the results of which were used as input to the analysis of the life of a highly stressed node.
Simcenter 3D software was used for the project.
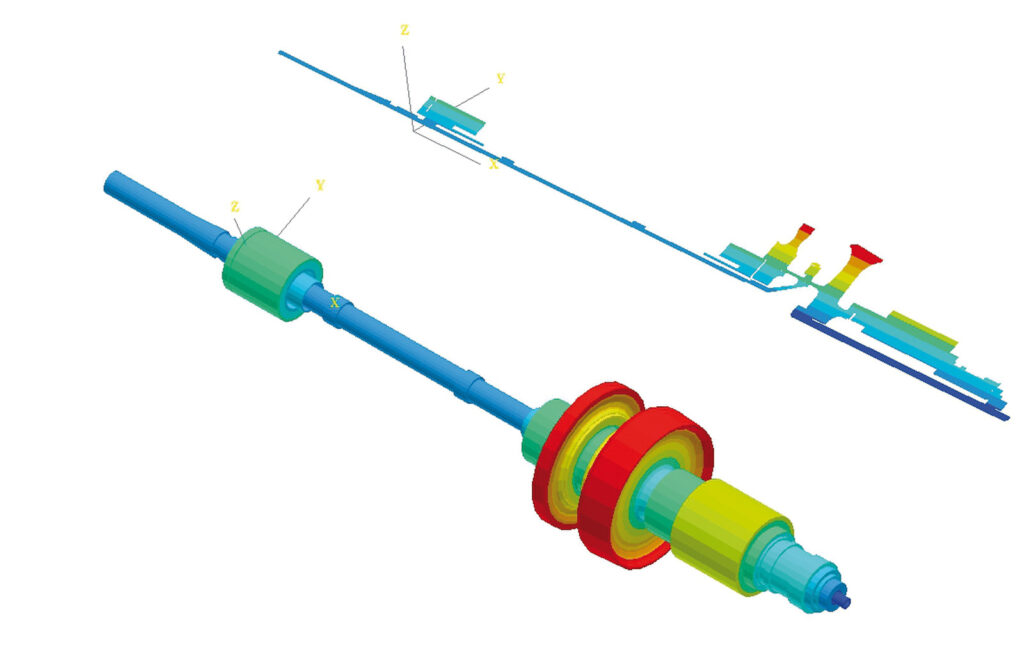
ORC unit turbine rotor dynamics calculation
Based on provided 3D geometric model of the rotor system, FE model for the calculation of rotor dynamics was created. The project resulted in a Cambell diagram, determination of critical speed and determination of sensitivity of critical speed to bearing stiffness. Unbalances according to ISO 1940 were included in the model.
Simcenter 3D software was used for the project.
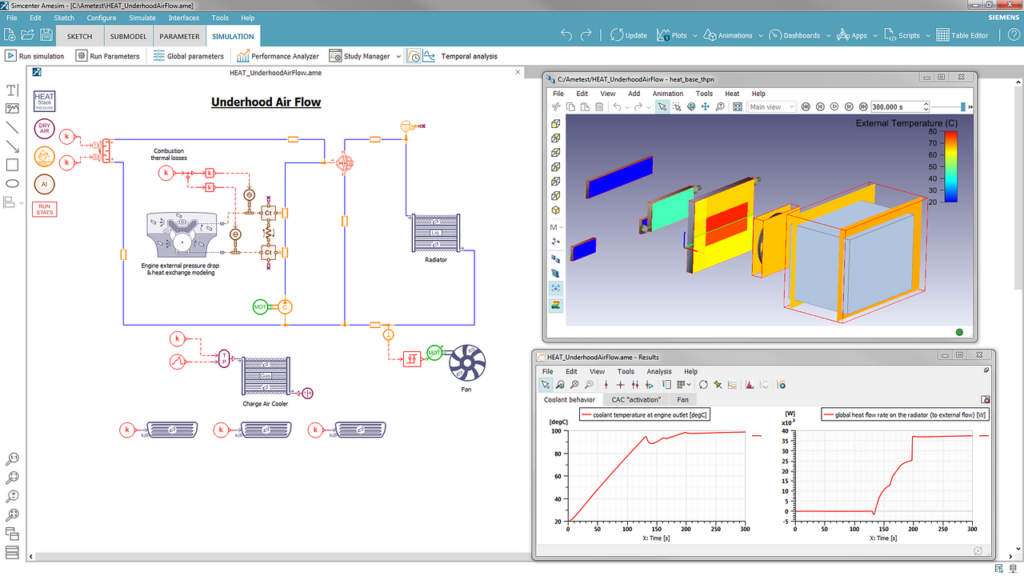
1D functional model of tractor engine cooling
As part of the project, a 1D model of the tractor cooling system was created, which allows predicting inlet and outlet temperatures of the water cooler and outlet temperatures of other heat exchangers. The project also included measurement of the heat exchangers.
Simcenter Amesim software was used for the project.
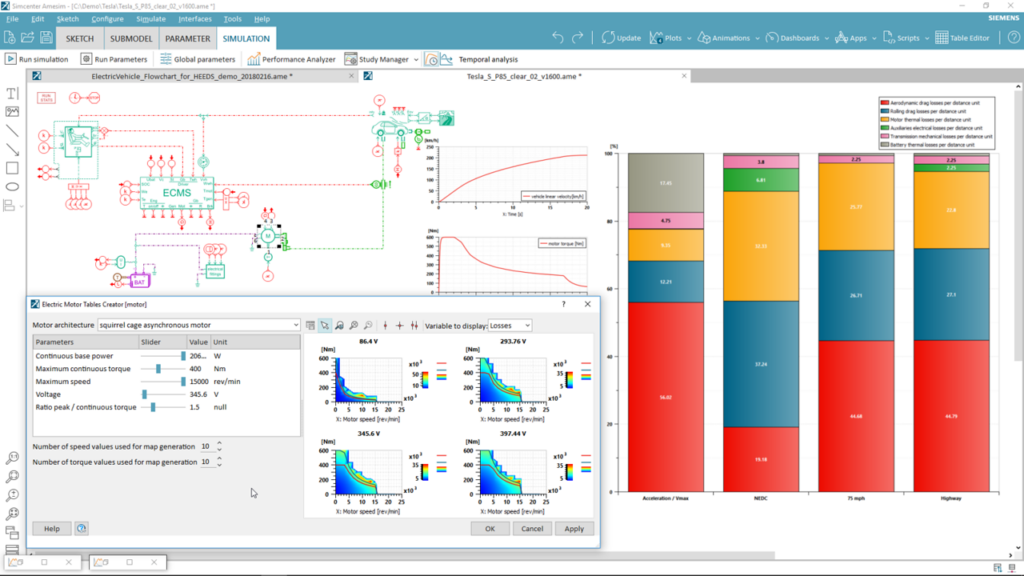
Calculation of energy balance of electric traction
Calculation of energy balance of electric traction
The aim of the analysis was to determine the benefits of electric traction with or without the use of a gearbox. The project was assessed in terms of efficiency, sizing and overall cost.
Software used: Simcenter Amesim, Simcenter MotorSolve.
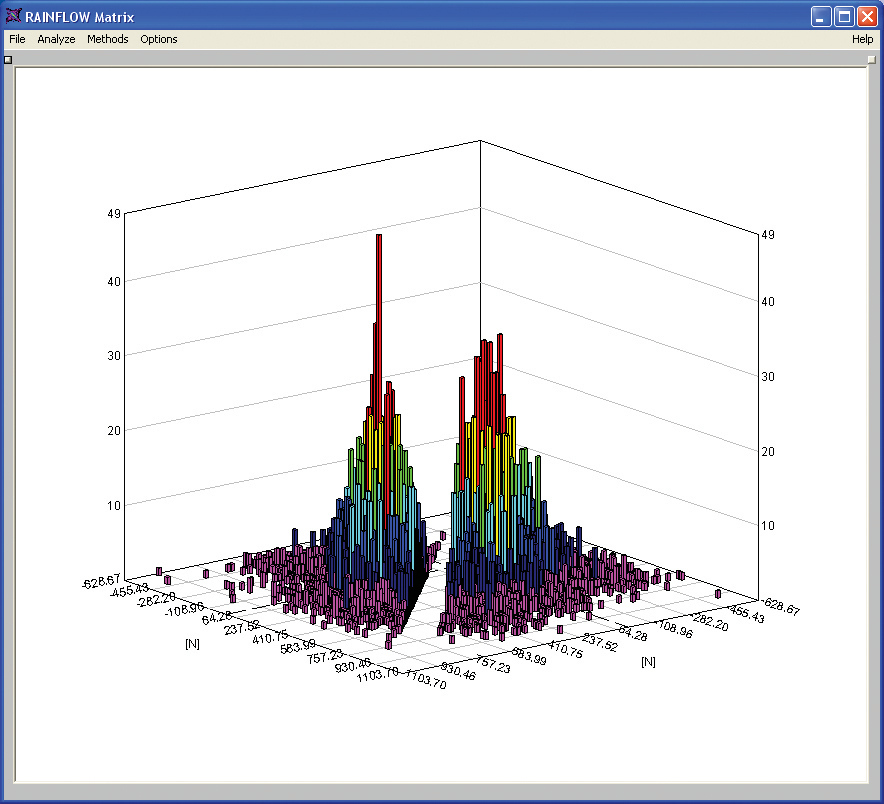
Fatigue analysis and analysis of crack propagation at turbine rotor
The fatigue analysis of the turbine rotor was performed on the basis of standard FE calculations. The possibility of crack initiation for defined operating conditions was assessed. The next step of the fatigue analysis was, by means of fracture mechanics, the assessment of the possibility of crack propagation in given operating conditions.
Software used: Simcenter 3D.
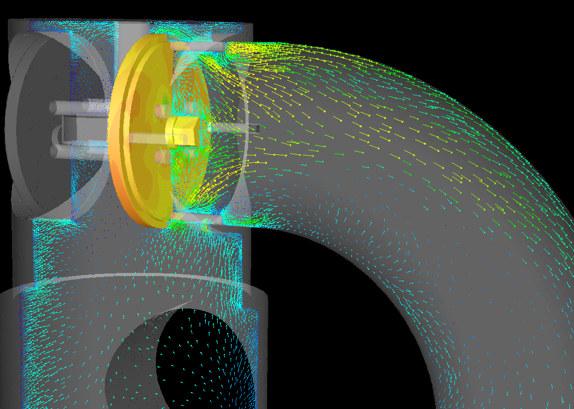
Three-way valve simulation
An analysis of the influence of pre-stressed bolts and the effect of oil inclusion on natural valve frequencies was performed.
This was followed by CFD analysis describing the effect of turbulent flow on valve design.
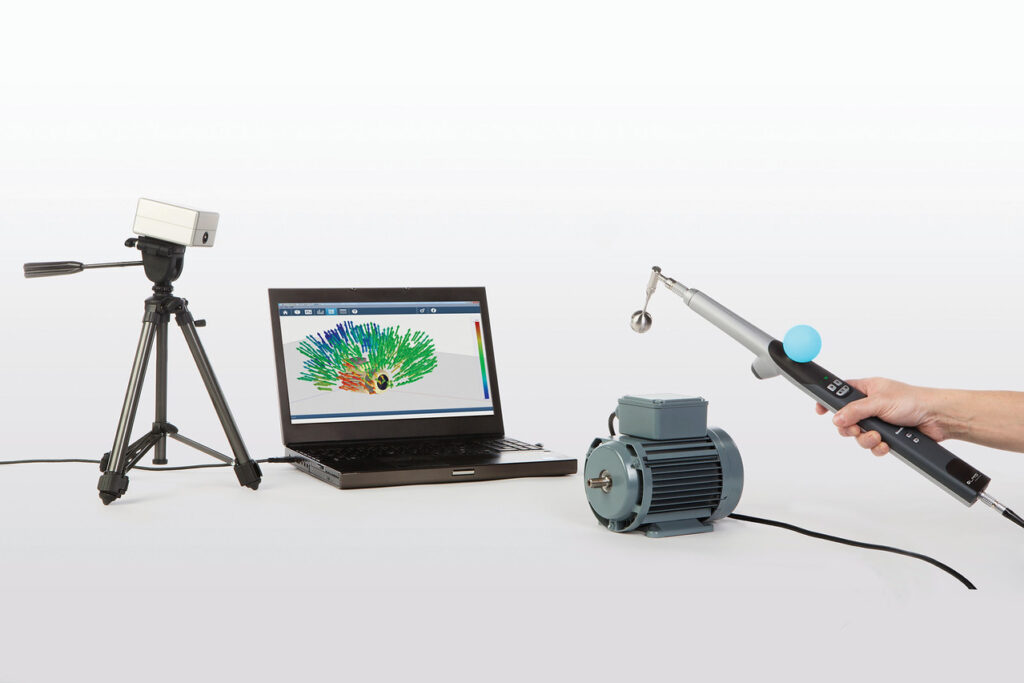
Measurement of electric motor noise and its optimization leading to noise reduction
Using the acoustic camera and the intensity probe the source of the electric motor noise was detected. This was followed by designing engine modifications to reduce noise.
Software used: Simcenter 3D.
Hardware used: Sound camera, intensity probe in conjunction with Simcenter SCADAS.
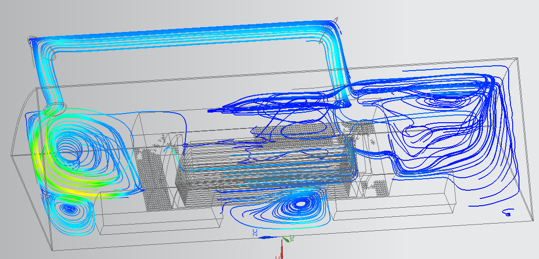
Transformer cooling
The aim of the CFD simulation was to calculate the temperature field of the oil and transformer parts and to analyze the current field.
Software used: Simcenter 3D.
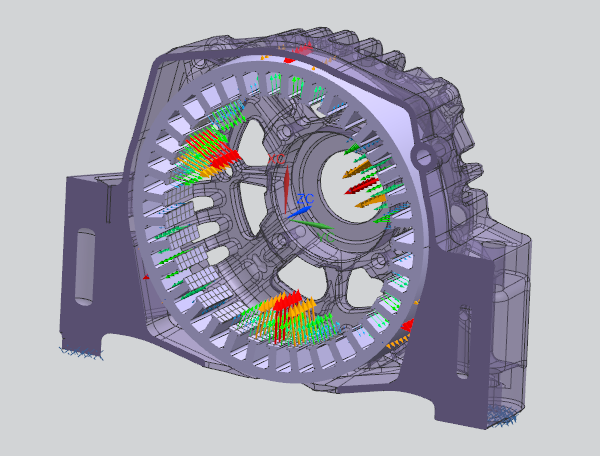
Analysis and optimization of electric motor
The aim of the analysis was to assess the electric motor in terms of efficiency and power. Results of the analysis was the electric motor efficiency map, detailed description of its behavior at defined operating points (torque ripple, magnetic induction and loss distribution) and determination of critical motor parts were determined. After the analysis we have done the optimization of the critical parts of the elekctromotor.
Software used: Simcenter MotorSolve, Simcenter Amesim.
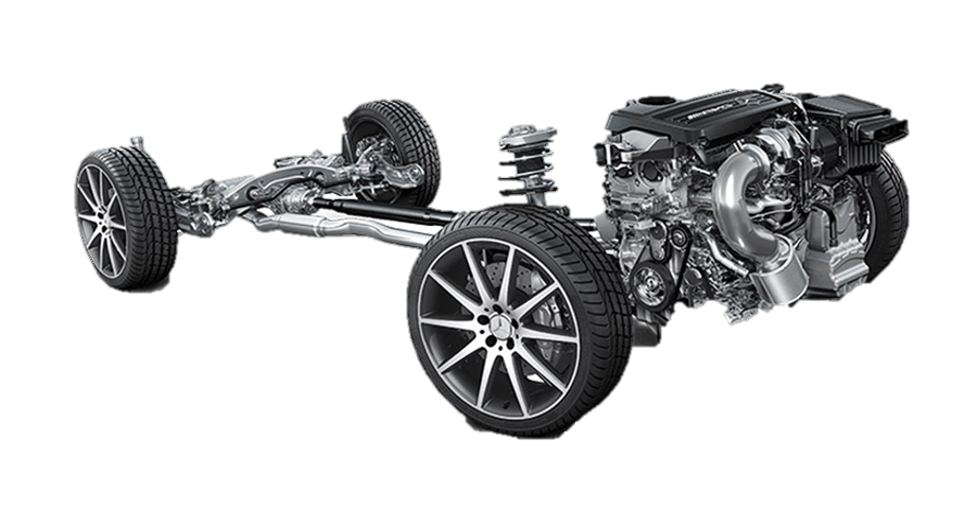
Design of electric traction
We participated in the project for the design of electrical traction from the initial definition of requirements, sizing, selection and development of individual components, to testing the produced prototype on a test stand.
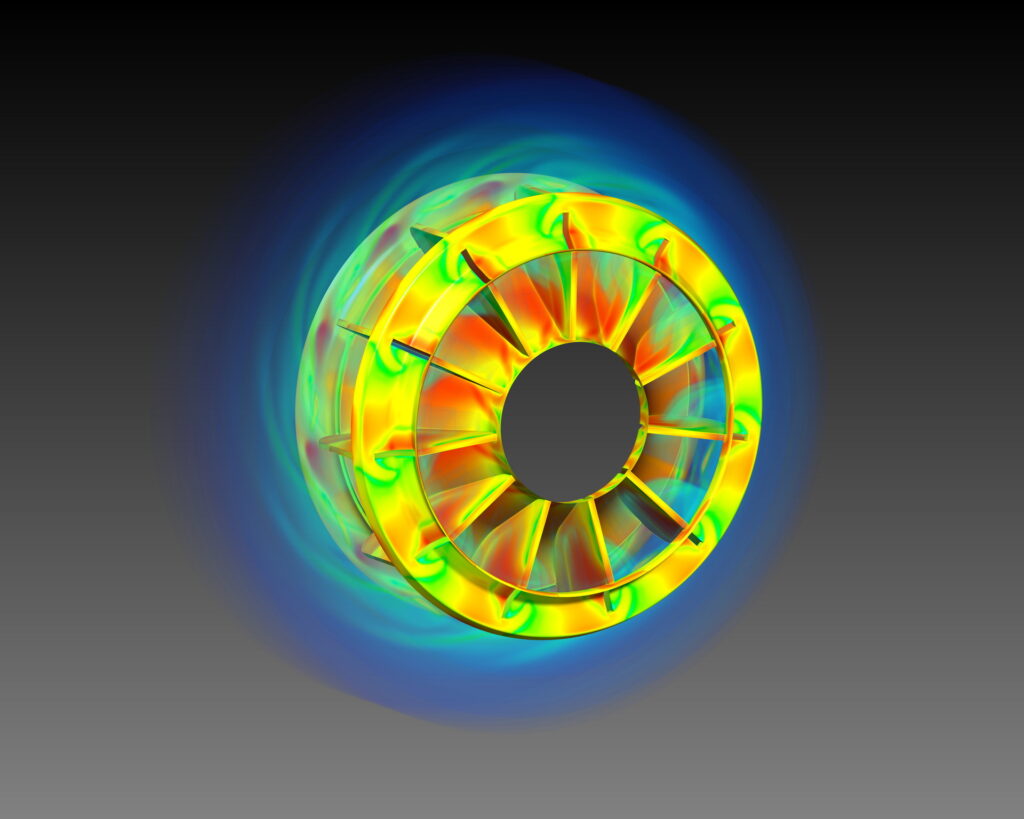
Aeroacoustic noise prediction of electric motor fan
The motivation of this project was to find and apply tools for prediction of noise of electric motor fan using CFD. Within this project, a methodology for predicting aeroacoustic noise of radial fan was developed, both by broadband method for quick determination of total sound pressure and by means of acoustic analogy enabling spectral analysis and determination of dominant noise frequencies.
The numerical model has been successfully validated based on experimental measurement data and has contributed to a more efficient and less noisy cooling design.
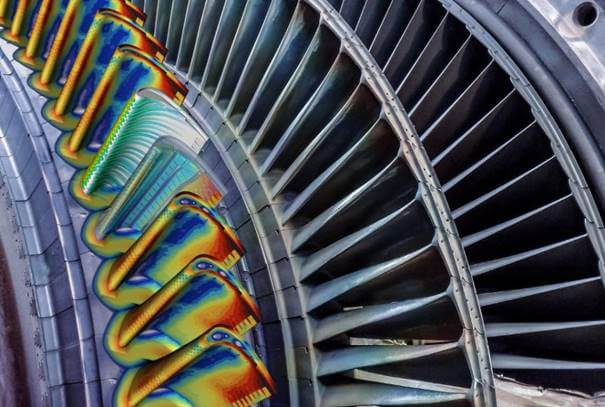
Optimization of ORC of the turbine stage
Based on the analytical design and CFD, the optimal shape parameters of the complete ORC unit were designed (spiral casing, distributor nozzles, impeller and casing lid).
The aim of optimization was shape design of individual parts with respect to pressure drop and efficiency.
The project’s successful challenge was to fine-tune the interaction of the nozzles and the impeller with respect to the shock wave rectification.
Software used: Simcenter STAR-CCM +, NX.
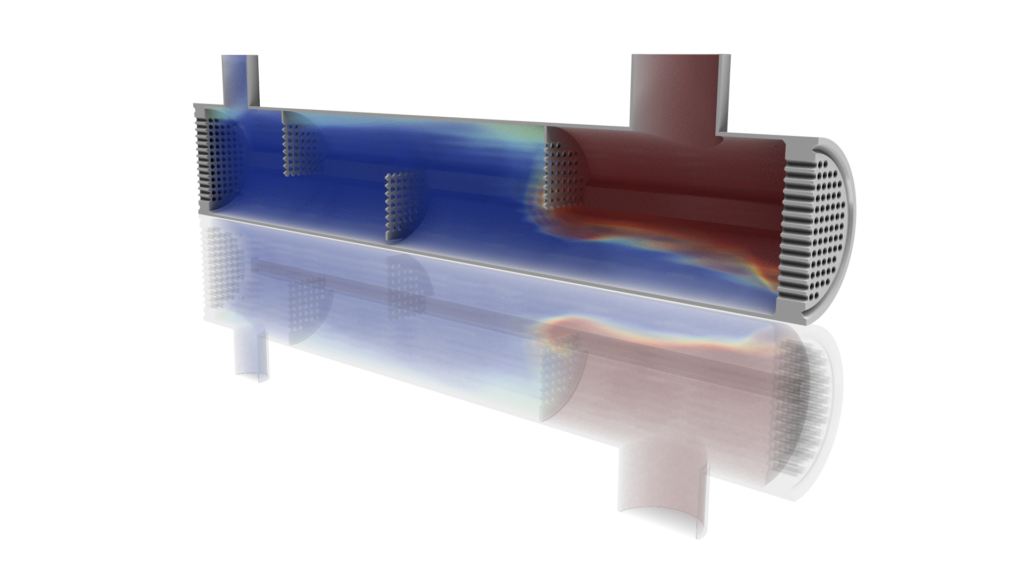
Thermal stress analysis of countercurrent capacitor including flow and condensation
For a significant client in the field of turbine industry, a CFD analysis of a countercurrent condenser was performed, including the transfer of heat into the walls and condensate formation and runoff on the surface of the cooling tubes. As a result, it was possible to accurately determine the thermal stress on the crossbars holding the cooling tubes, which led to subsequent application of the measures and improved heat resistance of the device.
Software used: Simcenter STAR-CCM +
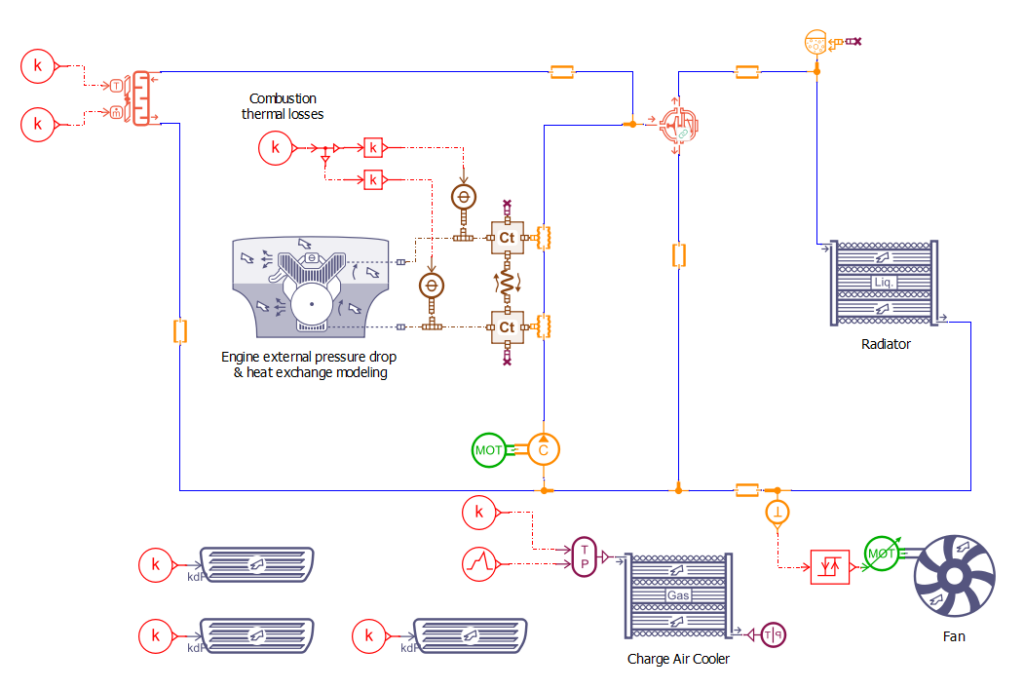
System simulation of the vehicle cooling circuit
In order to optimize cooling performance, a 1D model has been created incorporating a complete vehicle cooling circuit. To achieve the real behavior of the model, all heat exchangers in the engine compartment were included in the analysis and the interaction between them was given by their full or partial overlap. Calibration of the model was performed on the basis of experimental measurement of characteristics of individual heat exchangers, which was ensured in cooperation with a partner company. The model was then validated on the basis of data from standard tests performed by the manufacturer. Based on the results of the analysis, specific changes to the configuration of the heat sink location have been recommended leading to more efficient heat removal.
Software used:Simcenter Amesim
What else could you be interested in?
Simcenter Amesim Cooling System library